Aktualizacja 21 lipca 2025
Budowa maszyn produkcyjnych to złożony proces, który wymaga uwzględnienia wielu kluczowych elementów. W pierwszej kolejności warto zwrócić uwagę na konstrukcję mechaniczną, która jest fundamentem każdej maszyny. Obejmuje ona ramę, podzespoły oraz elementy nośne, które muszą być odpowiednio zaprojektowane, aby zapewnić stabilność i wytrzymałość. Kolejnym istotnym aspektem jest napęd, który może być elektryczny, hydrauliczny lub pneumatyczny. Wybór odpowiedniego napędu zależy od specyfiki maszyny oraz jej przeznaczenia. Ważnym elementem są także systemy sterowania, które umożliwiają precyzyjne zarządzanie pracą maszyny. W nowoczesnych rozwiązaniach często wykorzystuje się programowalne sterowniki logiczne (PLC), które zwiększają elastyczność i automatyzację procesów produkcyjnych. Nie można zapominać o bezpieczeństwie, dlatego każda maszyna powinna być wyposażona w odpowiednie zabezpieczenia oraz systemy awaryjne, które chronią operatorów przed potencjalnymi zagrożeniami.
Jakie technologie są wykorzystywane w budowie maszyn produkcyjnych
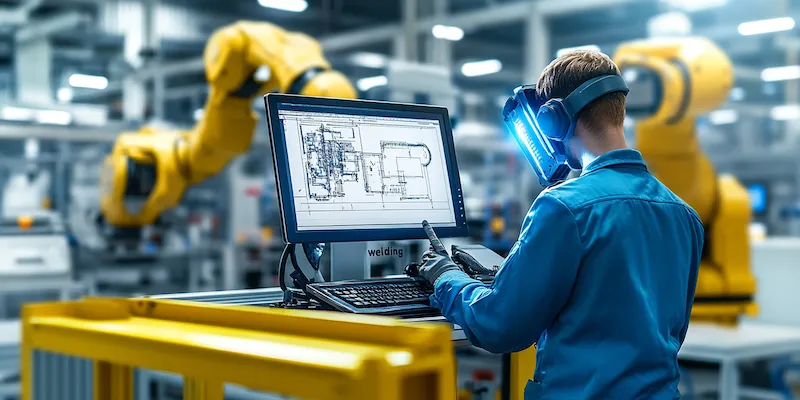
W dzisiejszych czasach budowa maszyn produkcyjnych opiera się na zaawansowanych technologiach, które znacznie poprawiają wydajność oraz jakość produkcji. Jednym z najważniejszych trendów jest automatyzacja procesów, która pozwala na zminimalizowanie udziału człowieka w rutynowych zadaniach. W tym kontekście roboty przemysłowe odgrywają kluczową rolę, ponieważ mogą wykonywać powtarzalne operacje z dużą precyzją i szybkością. Kolejnym istotnym aspektem jest zastosowanie technologii CAD/CAM, które umożliwiają projektowanie oraz wytwarzanie komponentów maszyn w sposób cyfrowy. Dzięki tym narzędziom inżynierowie mogą tworzyć skomplikowane modele 3D, co znacznie przyspiesza proces prototypowania oraz produkcji. Warto również zwrócić uwagę na rozwój materiałów kompozytowych i lekkich stopów metali, które są coraz częściej wykorzystywane w budowie maszyn ze względu na swoje korzystne właściwości mechaniczne i niską wagę.
Jakie są najczęstsze problemy w budowie maszyn produkcyjnych
Budowa maszyn produkcyjnych wiąże się z wieloma wyzwaniami i problemami, które mogą wpływać na efektywność całego procesu. Jednym z najczęstszych problemów jest niewłaściwe dobranie materiałów do konstrukcji maszyny. Użycie materiałów o niskiej jakości może prowadzić do szybszego zużycia się komponentów oraz obniżenia wydajności pracy. Kolejnym istotnym zagadnieniem są błędy projektowe, które mogą wynikać z niedostatecznej analizy wymagań technicznych lub braku doświadczenia zespołu projektowego. Takie błędy mogą prowadzić do poważnych usterek w działaniu maszyny oraz zwiększenia kosztów naprawy. Problemy mogą również pojawić się podczas montażu maszyny; niewłaściwe ustawienie podzespołów czy brak precyzyjnego wykonania może skutkować nieprawidłowym działaniem urządzenia. Dodatkowo, zmiany w wymaganiach klientów czy dynamiczny rozwój technologii mogą powodować konieczność modyfikacji już zaprojektowanych maszyn, co również stanowi wyzwanie dla inżynierów.
Jakie są przyszłościowe kierunki rozwoju budowy maszyn produkcyjnych
Przyszłość budowy maszyn produkcyjnych rysuje się w jasnych barwach dzięki ciągłemu postępowi technologicznemu oraz rosnącemu zapotrzebowaniu na innowacyjne rozwiązania w przemyśle. Jednym z kluczowych kierunków rozwoju jest dalsza automatyzacja procesów produkcyjnych, która ma na celu zwiększenie wydajności oraz redukcję kosztów operacyjnych. W tym kontekście rozwój sztucznej inteligencji oraz uczenia maszynowego otwiera nowe możliwości dla optymalizacji procesów i podejmowania decyzji na podstawie analizy dużych zbiorów danych. Również technologie związane z drukiem 3D stają się coraz bardziej popularne w budowie maszyn; pozwalają one na szybkie prototypowanie oraz produkcję skomplikowanych komponentów bez potrzeby stosowania tradycyjnych metod obróbczych. Zrównoważony rozwój staje się kolejnym ważnym trendem; producenci poszukują ekologicznych materiałów oraz energooszczędnych rozwiązań technologicznych, aby ograniczyć wpływ swojej działalności na środowisko naturalne.
Jakie są kluczowe aspekty projektowania maszyn produkcyjnych
Projektowanie maszyn produkcyjnych to proces, który wymaga staranności i przemyślanej strategii. Kluczowym aspektem jest zrozumienie specyfikacji technicznych oraz wymagań użytkowników, co pozwala na stworzenie maszyny, która będzie w pełni funkcjonalna i dostosowana do potrzeb rynku. W tym kontekście ważne jest przeprowadzenie analizy funkcjonalnej, która pomoże określić, jakie zadania maszyna ma realizować oraz jakie parametry są dla niej kluczowe. Kolejnym istotnym elementem jest ergonomia, czyli dostosowanie maszyny do potrzeb operatorów. Dobrze zaprojektowane stanowisko pracy powinno zapewniać komfort i bezpieczeństwo użytkowników, co przekłada się na efektywność ich pracy. Ważne jest także uwzględnienie aspektów związanych z konserwacją i serwisowaniem maszyny; projekt powinien umożliwiać łatwy dostęp do kluczowych komponentów w celu ich naprawy lub wymiany. Współczesne projektowanie maszyn coraz częściej korzysta z symulacji komputerowych, które pozwalają na testowanie różnych rozwiązań jeszcze przed rozpoczęciem produkcji.
Jakie są różnice między maszynami produkcyjnymi a tradycyjnymi urządzeniami
Maszyny produkcyjne różnią się od tradycyjnych urządzeń przede wszystkim pod względem zaawansowania technologicznego oraz zastosowania. Tradycyjne urządzenia często opierają się na prostych mechanizmach i manualnym sterowaniu, podczas gdy nowoczesne maszyny produkcyjne wykorzystują zaawansowane systemy automatyzacji oraz robotykę. To sprawia, że maszyny produkcyjne są w stanie wykonywać skomplikowane operacje z dużą precyzją i szybkością, co znacząco zwiększa wydajność procesów produkcyjnych. Kolejną różnicą jest elastyczność; nowoczesne maszyny często umożliwiają szybkie dostosowanie do zmieniających się potrzeb rynku oraz różnorodności produktów. Dzięki zastosowaniu technologii takich jak programowalne sterowniki czy interfejsy HMI (Human-Machine Interface), operatorzy mogą łatwo zmieniać parametry pracy maszyny bez konieczności jej przebudowy. Warto również zwrócić uwagę na kwestie związane z bezpieczeństwem; nowoczesne maszyny produkcyjne są wyposażone w szereg zabezpieczeń oraz systemów monitorujących, które chronią operatorów przed potencjalnymi zagrożeniami.
Jakie są wyzwania związane z utrzymaniem maszyn produkcyjnych
Utrzymanie maszyn produkcyjnych to kluczowy aspekt zapewniający ich długotrwałe i efektywne działanie. Jednym z głównych wyzwań jest konieczność regularnej konserwacji, która obejmuje zarówno przeglądy techniczne, jak i wymianę zużytych komponentów. Niezbędne jest opracowanie harmonogramu konserwacji, który uwzględnia specyfikę danej maszyny oraz intensywność jej użytkowania. Kolejnym problemem może być brak odpowiednich części zamiennych; w przypadku awarii maszyny czas przestoju może generować znaczne straty finansowe dla przedsiębiorstwa. Dlatego istotne jest posiadanie sprawdzonego dostawcy części zamiennych oraz prowadzenie odpowiednich zapasów. Warto również zwrócić uwagę na szkolenie personelu odpowiedzialnego za obsługę maszyn; niewłaściwe użytkowanie lub brak wiedzy na temat specyfiki danej maszyny mogą prowadzić do szybszego zużycia lub uszkodzenia sprzętu.
Jakie są korzyści płynące z inwestycji w nowoczesne maszyny produkcyjne
Inwestycja w nowoczesne maszyny produkcyjne przynosi wiele korzyści, które mogą znacząco wpłynąć na rozwój przedsiębiorstwa. Przede wszystkim nowoczesne technologie pozwalają na zwiększenie wydajności procesów produkcyjnych; dzięki automatyzacji i zastosowaniu robotów przemysłowych możliwe jest osiągnięcie wyższej jakości produktów przy jednoczesnym obniżeniu kosztów pracy. Ponadto nowoczesne maszyny charakteryzują się większą precyzją wykonania, co przekłada się na mniejsze straty materiałowe oraz lepszą jakość finalnych wyrobów. Inwestycje te mogą również przyczynić się do poprawy bezpieczeństwa pracy; nowoczesne urządzenia są wyposażone w zaawansowane systemy zabezpieczeń oraz monitorowania stanu technicznego, co minimalizuje ryzyko wystąpienia awarii czy wypadków. Dodatkowo posiadanie innowacyjnego parku maszynowego może stać się istotnym atutem konkurencyjnym na rynku; przedsiębiorstwa oferujące wysokiej jakości produkty są bardziej atrakcyjne dla klientów i mogą liczyć na większe zainteresowanie ze strony kontrahentów.
Jakie są najnowsze trendy w budowie maszyn produkcyjnych
Najnowsze trendy w budowie maszyn produkcyjnych koncentrują się wokół innowacyjnych technologii oraz zrównoważonego rozwoju. Jednym z najważniejszych kierunków jest automatyzacja procesów, która pozwala na zwiększenie efektywności oraz redukcję kosztów operacyjnych. W tym kontekście rozwój sztucznej inteligencji oraz uczenia maszynowego otwiera nowe możliwości dla optymalizacji procesów i podejmowania decyzji na podstawie analizy dużych zbiorów danych. Również technologie związane z drukiem 3D stają się coraz bardziej popularne w budowie maszyn; pozwalają one na szybkie prototypowanie oraz produkcję skomplikowanych komponentów bez potrzeby stosowania tradycyjnych metod obróbczych. Zrównoważony rozwój staje się kolejnym ważnym trendem; producenci poszukują ekologicznych materiałów oraz energooszczędnych rozwiązań technologicznych, aby ograniczyć wpływ swojej działalności na środowisko naturalne.
Jakie umiejętności są potrzebne do pracy przy budowie maszyn produkcyjnych
Praca przy budowie maszyn produkcyjnych wymaga szerokiego zakresu umiejętności technicznych oraz interpersonalnych. Kluczową umiejętnością jest znajomość zasad mechaniki oraz elektroniki, ponieważ większość nowoczesnych maszyn opiera się na skomplikowanych systemach mechanicznych i elektronicznych. Inżynierowie zajmujący się projektowaniem maszyn powinni być biegli w obsłudze oprogramowania CAD/CAM, które umożliwia tworzenie modeli 3D oraz symulacji działania urządzeń. Umiejętność analizy danych również staje się coraz bardziej istotna; inżynierowie muszą potrafić interpretować wyniki testów i analizować dane dotyczące wydajności maszyn w celu ich optymalizacji. Również umiejętności komunikacyjne są niezbędne; praca nad projektem często wymaga współpracy z innymi specjalistami, takimi jak technicy czy menedżerowie projektów. Dodatkowo znajomość języka angielskiego staje się coraz bardziej istotna w kontekście globalizacji przemysłu; wiele dokumentacji technicznych jest dostępnych tylko w tym języku.