Aktualizacja 14 lipca 2025
Destylatory przemysłowe mają szerokie zastosowanie w różnych branżach, co czyni je niezwykle istotnym elementem wielu procesów produkcyjnych. W przemyśle chemicznym destylatory służą do separacji substancji chemicznych na podstawie różnic w temperaturze wrzenia. Dzięki temu można uzyskać czyste składniki, które są niezbędne do produkcji leków, kosmetyków czy detergentów. W przemyśle spożywczym destylatory wykorzystywane są do produkcji alkoholu, olejków eterycznych oraz aromatów. Proces destylacji pozwala na uzyskanie wysokiej jakości produktów, które są wolne od zanieczyszczeń i mają intensywny smak oraz zapach. W sektorze energetycznym destylatory znajdują zastosowanie w rafinacji ropy naftowej, gdzie umożliwiają wydobycie różnych frakcji paliwowych, takich jak benzyna, olej napędowy czy nafta.
Jakie są kluczowe komponenty destylatorów przemysłowych
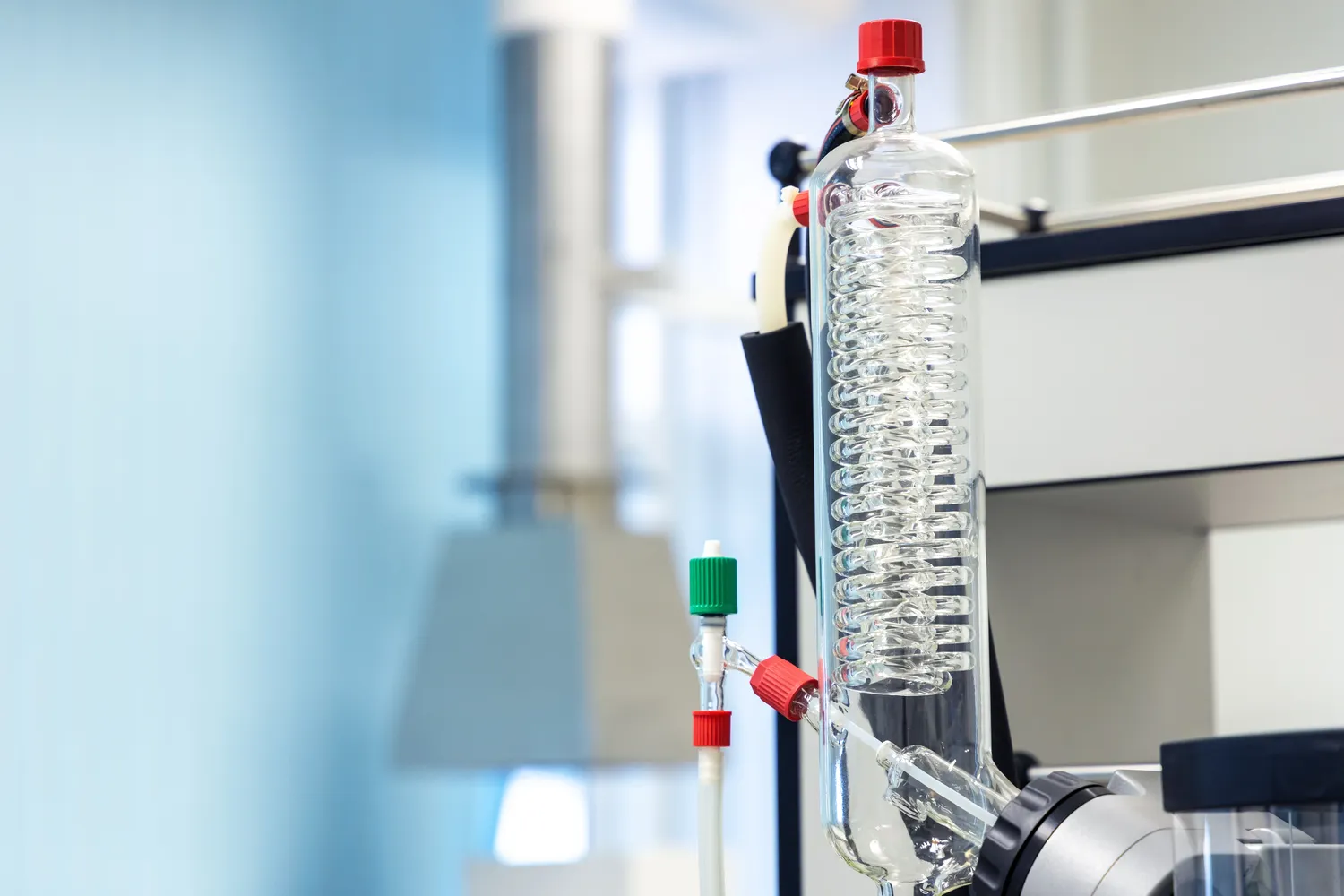
Kluczowe komponenty destylatorów przemysłowych odgrywają fundamentalną rolę w efektywności i wydajności procesu destylacji. Podstawowym elementem jest kolumna destylacyjna, która jest miejscem separacji składników na podstawie ich temperatury wrzenia. Wewnątrz kolumny znajdują się różne elementy, takie jak półki czy packingi, które zwiększają powierzchnię kontaktu między parą a cieczą, co sprzyja lepszej separacji substancji. Innym istotnym komponentem jest kondensator, który schładza parę i przekształca ją z powrotem w ciecz. Kondensatory mogą mieć różne konstrukcje, w zależności od wymagań procesu i rodzaju przetwarzanych substancji. Dodatkowo ważnym elementem jest zbiornik na produkt końcowy, który musi być odpowiednio zaprojektowany, aby zapewnić łatwy dostęp do gotowego produktu oraz możliwość jego dalszego przetwarzania lub magazynowania.
Jakie są najnowsze technologie w dziedzinie destylacji przemysłowej
Najnowsze technologie w dziedzinie destylacji przemysłowej koncentrują się na zwiększeniu efektywności energetycznej oraz redukcji kosztów operacyjnych. Jednym z najważniejszych trendów jest rozwój systemów destylacji membranowej, które oferują alternatywę dla tradycyjnych metod. Technologia ta pozwala na separację składników przy użyciu membran selektywnych, co znacznie zmniejsza zużycie energii i eliminuje potrzebę stosowania wysokich temperatur. Kolejnym innowacyjnym rozwiązaniem są systemy hybrydowe łączące różne metody separacji, takie jak destylacja i ekstrakcja cieczy cieczą. Takie podejście pozwala na uzyskanie lepszej jakości produktów oraz zwiększenie wydajności procesów. Również automatyzacja procesów destylacyjnych staje się coraz bardziej powszechna dzięki zastosowaniu zaawansowanych systemów monitorowania i sterowania, które umożliwiają bieżącą analizę danych oraz optymalizację pracy urządzeń.
Jakie są koszty związane z zakupem i eksploatacją destylatorów przemysłowych
Koszty związane z zakupem i eksploatacją destylatorów przemysłowych mogą być znaczące i powinny być starannie analizowane przed podjęciem decyzji o inwestycji. Koszt zakupu samego urządzenia zależy od jego wielkości, rodzaju technologii oraz specyfiki zastosowań. W przypadku skomplikowanych systemów z zaawansowanymi funkcjami automatyzacji cena może być znacznie wyższa niż w przypadku prostszych modeli. Oprócz kosztu zakupu należy uwzględnić także wydatki związane z instalacją oraz uruchomieniem urządzenia, które mogą wymagać specjalistycznej wiedzy i dodatkowych zasobów. Koszty eksploatacyjne obejmują zużycie energii elektrycznej, konserwację oraz serwisowanie urządzenia. Regularne przeglądy techniczne są niezbędne dla zapewnienia długotrwałej efektywności działania destylatora oraz uniknięcia awarii, które mogą prowadzić do dodatkowych kosztów związanych z przestojami produkcyjnymi.
Jakie są kluczowe czynniki wpływające na wybór destylatora przemysłowego
Wybór odpowiedniego destylatora przemysłowego jest procesem skomplikowanym i wymaga uwzględnienia wielu kluczowych czynników, które mogą znacząco wpłynąć na efektywność produkcji. Przede wszystkim należy zwrócić uwagę na rodzaj substancji, które będą poddawane destylacji. Różne materiały mają różne właściwości fizyczne, takie jak temperatura wrzenia czy lepkość, co może determinować wybór konkretnego typu destylatora. Kolejnym istotnym czynnikiem jest wydajność urządzenia, która powinna być dostosowana do potrzeb produkcyjnych firmy. Warto również rozważyć aspekty związane z automatyzacją procesu, ponieważ nowoczesne systemy sterowania mogą znacznie zwiększyć efektywność operacyjną oraz zmniejszyć ryzyko błędów ludzkich. Należy także wziąć pod uwagę koszty eksploatacyjne, takie jak zużycie energii oraz potrzeby konserwacyjne, które mogą wpływać na całkowity koszt użytkowania urządzenia.
Jakie są różnice między destylatorami ciągłymi a wsadowymi
Destylatory przemysłowe można podzielić na dwie główne kategorie: destylatory ciągłe oraz wsadowe, które różnią się zasadniczo sposobem działania oraz zastosowaniem. Destylatory ciągłe są zaprojektowane do nieprzerwanego przetwarzania surowców, co sprawia, że są idealne dla dużych zakładów produkcyjnych, gdzie wymagana jest wysoka wydajność i stała jakość produktów. W tego typu systemach surowce są wprowadzane do kolumny destylacyjnej w sposób ciągły, a produkty uboczne są usuwane równolegle. Z kolei destylatory wsadowe działają na zasadzie przetwarzania określonej ilości surowca w jednym cyklu, co sprawia, że są bardziej elastyczne i mogą być stosowane do produkcji mniejszych partii różnych produktów. Tego rodzaju urządzenia są często wykorzystywane w laboratoriach oraz małych zakładach produkcyjnych, gdzie różnorodność produktów jest kluczowa.
Jakie są najczęstsze problemy związane z eksploatacją destylatorów przemysłowych
Eksploatacja destylatorów przemysłowych wiąże się z wieloma wyzwaniami i problemami, które mogą wpłynąć na efektywność procesu oraz jakość finalnych produktów. Jednym z najczęstszych problemów jest osadzanie się zanieczyszczeń wewnątrz kolumny destylacyjnej, co prowadzi do spadku wydajności separacji i obniżenia jakości produktów. Regularne czyszczenie oraz konserwacja urządzeń są niezbędne dla utrzymania ich w dobrym stanie technicznym. Innym istotnym problemem może być niewłaściwe ustawienie parametrów pracy destylatora, takich jak temperatura czy ciśnienie, co może prowadzić do nieefektywnej separacji składników. Warto również zwrócić uwagę na kwestie związane z bezpieczeństwem pracy, ponieważ procesy destylacyjne często wiążą się z wysokimi temperaturami oraz ciśnieniem, co stwarza ryzyko wystąpienia awarii lub wypadków.
Jakie są korzyści wynikające z inwestycji w nowoczesne destylatory przemysłowe
Inwestycja w nowoczesne destylatory przemysłowe przynosi wiele korzyści, które mogą znacząco wpłynąć na konkurencyjność przedsiębiorstwa na rynku. Przede wszystkim nowoczesne urządzenia charakteryzują się wyższą efektywnością energetyczną, co przekłada się na niższe koszty operacyjne oraz mniejsze zużycie surowców. Dzięki zastosowaniu zaawansowanych technologii możliwe jest osiągnięcie lepszej jakości produktów końcowych oraz ich większej czystości chemicznej. Nowoczesne systemy automatyzacji pozwalają na bieżące monitorowanie parametrów pracy destylatora oraz szybką reakcję na ewentualne odchylenia od normy, co zwiększa bezpieczeństwo i stabilność procesu produkcyjnego. Dodatkowo inwestycje w nowe technologie mogą przyczynić się do poprawy wizerunku firmy jako innowacyjnego producenta dbającego o środowisko naturalne poprzez ograniczenie emisji szkodliwych substancji oraz zmniejszenie zużycia energii.
Jakie są wymagania prawne dotyczące użytkowania destylatorów przemysłowych
Użytkowanie destylatorów przemysłowych wiąże się z koniecznością przestrzegania szeregu wymagań prawnych i regulacji dotyczących ochrony środowiska oraz bezpieczeństwa pracy. W wielu krajach istnieją przepisy regulujące emisję substancji szkodliwych do atmosfery oraz normy dotyczące jakości produktów końcowych. Firmy zajmujące się produkcją chemiczną czy spożywczą muszą spełniać określone standardy sanitarno-epidemiologiczne, które mają na celu zapewnienie bezpieczeństwa konsumentów. Ponadto użytkownicy destylatorów muszą przestrzegać przepisów dotyczących ochrony zdrowia pracowników, co obejmuje odpowiednie szkolenia oraz wdrażanie procedur bezpieczeństwa w miejscu pracy. W przypadku awarii lub incydentów związanych z użytkowaniem urządzeń konieczne jest zgłoszenie zdarzenia odpowiednim organom nadzorującym.
Jakie są przyszłościowe kierunki rozwoju technologii destylacji przemysłowej
Przyszłościowe kierunki rozwoju technologii destylacji przemysłowej koncentrują się na innowacjach mających na celu zwiększenie efektywności procesów oraz minimalizację ich wpływu na środowisko naturalne. Jednym z najważniejszych trendów jest rozwój technologii wykorzystujących odnawialne źródła energii do zasilania procesów destylacyjnych. Dzięki temu możliwe będzie ograniczenie emisji gazów cieplarnianych oraz zmniejszenie zależności od paliw kopalnych. Kolejnym kierunkiem rozwoju jest integracja systemów destylacyjnych z innymi procesami chemicznymi w ramach tzw. biorefineryjnych podejść do produkcji surowców chemicznych i energetycznych. Takie podejście pozwala na maksymalne wykorzystanie zasobów i minimalizację odpadów poprzez recykling materiałów wtórnych. Również rozwój sztucznej inteligencji i analizy danych ma potencjał do rewolucjonizacji procesów destylacyjnych poprzez optymalizację parametrów pracy urządzeń w czasie rzeczywistym oraz przewidywanie awarii zanim one nastąpią.